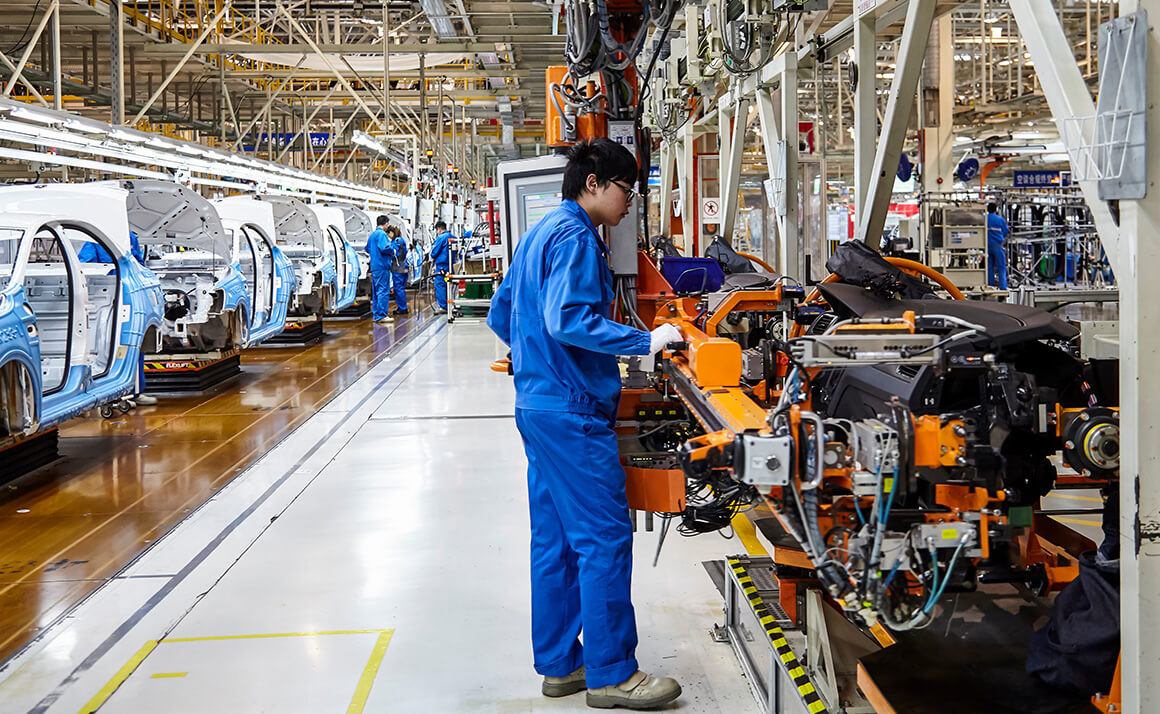
Moving manufacturing
The COVID-19 pandemic brought home to consumers and manufacturers that it is unwise to keep all your eggs in one basket.
China’s dominant position as the workshop of the world meant its lockdown seriously disrupted global supply chains, suggesting manufacturers ought to investigate alternative locations. Thus Asian and global manufacturers have been looking to diversify their operations across multiple markets and in some cases looking to move some production back home.
Prior to the pandemic, two other factors were driving this diversification. The US-China trade war, which seems set to continue regardless of the result of the US presidential election, led to increased tariffs on Chinese goods and rising wages in China mean it is no longer as cheap to build there as it once was.
So far, the movements have been fairly marginal: China remains a manufacturing powerhouse and in possession of the world’s largest skilled labour force. It also has a huge consumer market to serve. However, diversifying offshoring and ‘reshoring’ may have significant positive effect on other Asian nations.
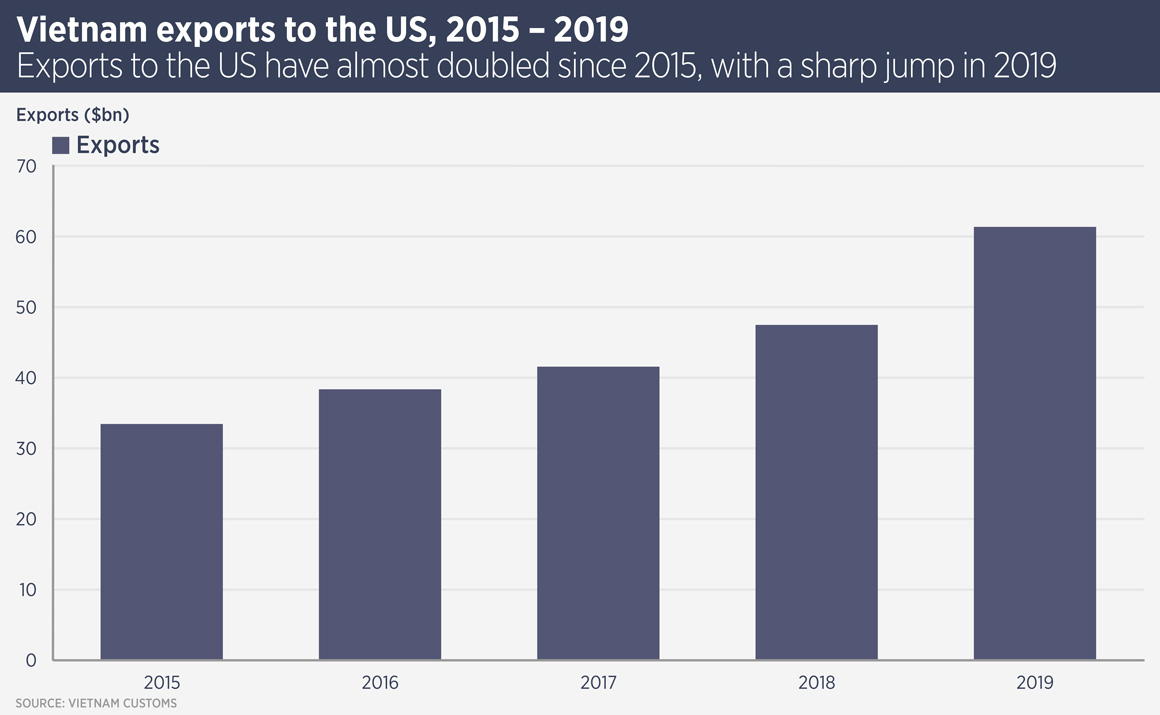
The prime beneficiary has been Vietnam, which saw its exports to the US increase nearly 30% in 2019. It has 336 industrial parks, of which 75 are under construction, indicating sharp supply growth, and developers are expecting more manufacturing to move from China this year and next. Companies such as Apple, Pegatron, and Foxconn have announced the shifting of some manufacturing to Vietnam.
Troy Griffiths, deputy managing director, Savills Vietnam says: “A China + 1 model may be increasingly pursued by manufacturers, which would result in greater demand for Vietnam industrial space, as corporations seek to mitigate risk and diversify locations. Industrial continues to be the ‘poster child’ for real estate, with mounting enquiries and heightened capital market activity.”
Global investors are keen to take advantage of Vietnam’s upswing; in August, logistics developer and fund manager Logos announced a new $350m Vietnam venture in partnership with an institutional investor. “Being able to establish this new venture in the midst of the COVID-19 pandemic is testament to Vietnam’s exciting growth story, which is driven by the global trade wars, decentralisation of supply chains and a natural evolution of this market,” says Trent Iliffe, managing director and co-CEO of Logos.
Meanwhile Japan, which has allocated $2.2bn to relocate manufacturing out of China, has announced that 15 companies will be moving manufacturing to Vietnam. The bulk of this cash, however, is intended to bring Japanese production back home.
Tetsuya Kaneko, head of research at Savills Japan, says: “Even before the spat between the US and China intensified, several manufacturers had already returned to Japan due to increasing labour costs in both China and other emerging economies, growing household incomes in emerging markets where consumers want to see a “made in Japan” tag and burgeoning inbound demand.
“As such, with more manufacturers going down the reshoring route, it should have a positive impact on the Japanese real estate market, albeit not a significant one.” However, Kaneko adds, Japan’s ongoing labour shortage and a lack of land for new factories may dampen appetite for reshoring, while “the importance of the Chinese consumer means manufacturers will retain production facilities close to the target market.”
The same problems exist for ‘reshoring’ South Korean firms, says JoAnn Hong, head of research at Savills Korea. They too want to keep selling goods to China and find their domestic land and labour too expensive. Like Japanese firms, they find Vietnam a good low-cost option. Any reshoring will have “not much effect on real estate,” she says.
The industrial market gaining the most from reshoring is Taiwan’s. Last year, the government announced a three year plan for attracting Taiwanese businesses back home and so far more than 550 companies have committed to invest $50bn in their home market.
To aid their return, Taiwan’s National Development Council is offering rent-free periods in state industrial zones and adapting the planning system to allow for more density in redeveloped industrial land. The effect on the investment market has been dramatic. Industrial property usually accounts for around 20% of transaction volumes, but in the first half of 2020, it accounted for 56%. Industrial land prices have risen 40% over the past five years, Savills data show.
“Owing to the policy encouraging intensification of industrial land and manufacturing industry moving back to Taiwan, developers are looking for old factories in the north of Taiwan to redevelop as more modern factories,” says Erin Ting, head of research at Savills Taiwan.
Further reading:
Savills Vietnam
Contact us:
Troy Griffiths | Simon Smith | Tetsuya Kaneko | JoAnn Hong | Erin Ting